LED Electronic Screen | High Definition Display Solutions to Light Up Your Every Moment
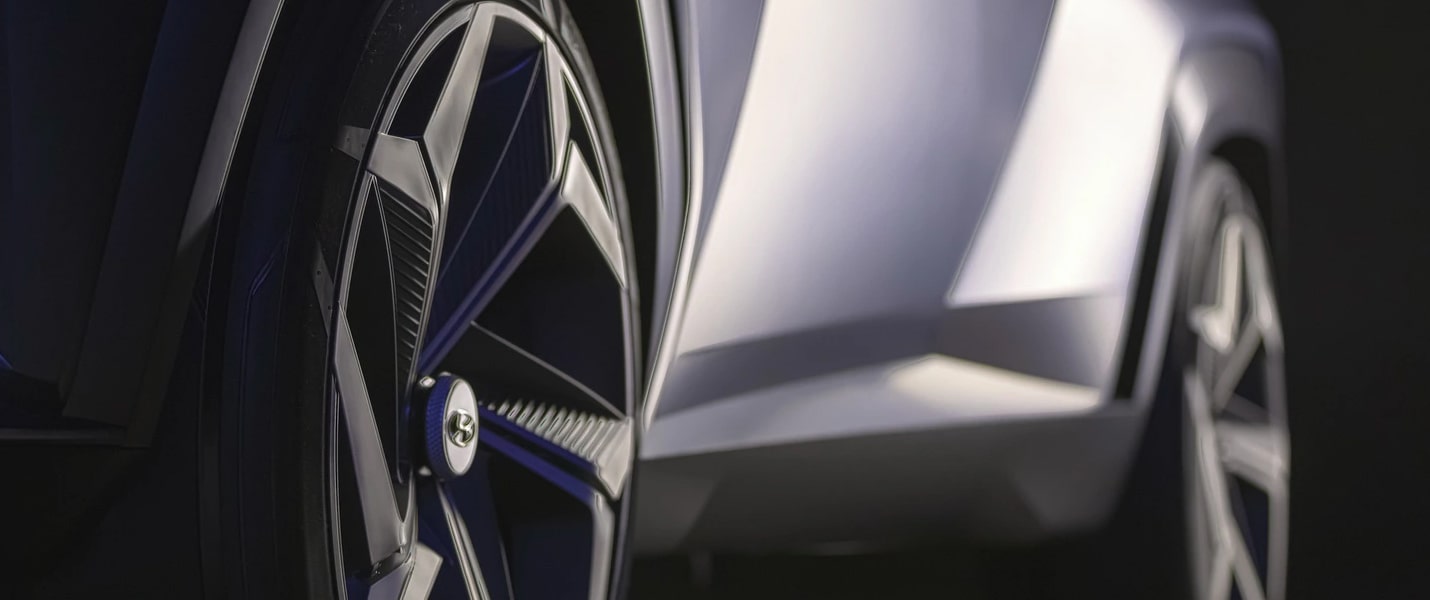
How to handle air bubbles after installing a Flexible LED Transparent Screen?
Due to the ultra-thin, flexible and other characteristics of the Flexible LED Transparent Screen, the installation of improper operation is prone to air bubbles, affecting the display effect and even life. This article will systematically analyze the causes of air bubbles, provide “first aid + prevention” full-process program to help you quickly solve the problem!
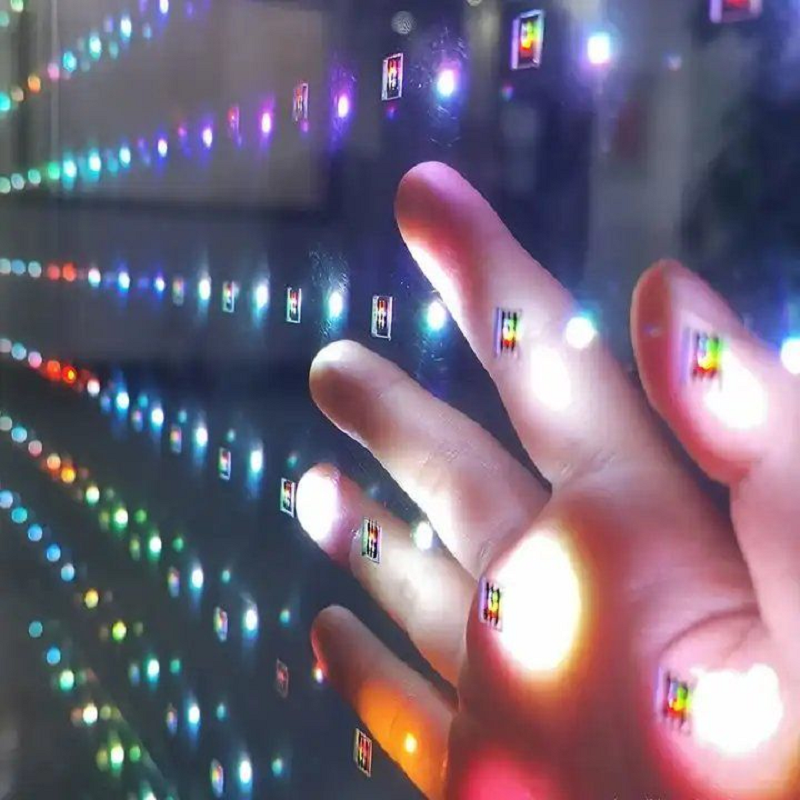
First, the Flexible LED Transparent Screen bubble causes analysis
- Surface cleaning is not complete
- Dust, oil or small particles remain, resulting in the adhesive layer and the substrate can not be completely affixed.
- Uneven laminating speed
- Tear the film at a tilted angle or too fast, the air is not discharged in time.
- Environmental temperature and humidity out of control
- Low temperature (<10℃), poor adhesive fluidity, high humidity (>80%), easy to condense water vapor.
- Uneven thickness of adhesive layer
- Uneven glue coating, localized formation of cavities.
- Extrusion interference
- Mistake touch or tool scraping after lamination, resulting in secondary displacement.
Second,Steps for dealing with crystal film screen bubbles in different scenarios
- Small bubbles (diameter <2mm)
- Step 1: Preheat the bubble area with a hot air gun at 40°C (for 10 seconds).
- Step 2: Slowly scrape from the edge of the bubble to the center, forcing air out from the side.
- Step 3: If traces remain, gently wipe the surface with a dust-free cloth dipped in a small amount of bubble remover.
- Large air bubbles (diameter > 2mm)
- Step 1: Drill holes (0.3mm micro holes, avoiding the display area) at the edge of the bubble.
- Step 2: Inject the defoamer into the hole with a syringe and leave it for 1 minute to dissolve the adhesive layer.
- Step 3: Heat to 50°C and push outward with a scraper until the bubbles disappear.
- Step 4: UV curing lamp irradiation for 10 seconds to seal the micro-hole (no UV lamp can be used to cover the transparent adhesive temporarily).
- Stubborn bubbles
- Scenario: After curing glue or repeated bubbles.
- Solution: Partial peeling and re-pasting – cut the bubble area (reserve 2mm margin), reapply adhesive and secondary lamination.
Finally,Four core skills to prevent air bubbles
- Environment Control
- Place the crystal film screen and the substrate in the same temperature and humidity environment 24 hours before installation (25℃/50%RH recommended).
- Slow and precise lamination
- Adopt the “roller-assisted method”: use a silicone roller to press together at a constant speed of 5cm/s.
- Glue selection
- High viscosity adhesive (>2000cps) for flat surfaces, low viscosity adhesive (500-1000cps) for curved surfaces.
- Tool Upgrade
- Use vacuum laminator or defoamer to eliminate micro bubbles.
Crystal film screen bubble problem needs to be solved from environmental control, process optimization, tool upgrading three aspects.
If you need customized installation solutions or technical engineers to visit your company, please contact us!